Comforts at the coalface
How shipyards are mitigating the rigorous demands of refit on crew…
Photo: Amico & Co / Freaklance
There’s no denying that superyacht refit projects can be very intense for all involved – from captains and project managers, to shipyards, suppliers and sub-contractors.
Among a myriad of factors that have to be brought to bear for everyone to work effectively together during what can be highly pressurised periods in the rush to meet those all-important deadlines – and remain, as far as possible, within budget – there’s another vital issue that is not always considered during this time: the well-being of superyacht crew.
Here, we speak to experienced crew and shipyards to discover more about the day-to-day reality of working on refit projects …
A change of pace
Firstly, whatever the size of the vessel and/or scope of the works being undertaken, it’s undeniable that launching into a refit project at a shipyard represents a major shift in working patterns and lifestyle for superyacht crew across all departments.
Most obviously, crew are no longer travelling the world between beautiful exotic destinations but instead find themselves working ashore, often in cold, wet and somewhat industrial locations for prolonged periods.
This can be an uncomfortable and gruelling experience. Andrea Nicholas, a chief stewardess/interior manager with more than 20 years’ experience in yachting, explains, “A lot of crew find it difficult as they are either living in apartments ashore in a country where they don’t speak the language [such as Germany, France or Spain], or they are living on the boat during the refit, which can be an uncomfortable, very busy work site, often without air conditioning, heating, running water or toilets on board.
“For some crew this is the first time they have lived on their own and [they] find it difficult adjusting and generally having to cook for themselves and the usual tasks we take for granted working on a yacht.”
Major refits, including paint jobs and structural modifications, often require that crew stay in onshore accommodation for at least part of the works period. Photo: Amico & Co / Freaklance.
In terms of working hours during refit projects, despite the fact that crew are no longer expected to undertake the extremely long hours which are part and parcel of guest trips, this does not mean that they get much rest.
Carol Benbrook, captain on board the 52-metre Palmer Johnson yacht Sanam, says: “Yard periods can be very demanding on the crew. You might imagine that you’re going to have a nine-to-five job and have your evenings and weekends free, but most of the time you just about get home in time to have dinner and would be lucky to have a quick bit of exercise before bed. There can be a lot of pressure on the crew because the yard period is often so condensed and we are trying to get in and out as soon as possible.”
Indeed, as Benbrook highlights, for those in senior crew positions in particular, there can be many plates to juggle during refit periods. “Take, for example, the chief engineer. They might be going from working with AV/IT, back down to replacing valves or sourcing equipment, working with suppliers and yard employees, supporting juniors, watching quality control for shaft alignment and much more – and then they must report on everything they have done that day. They have to be there when the yard opens in the morning and often can’t go home until after the last contractor.”
Communication is key
Naturally, when the financial and other stakes of a project are so high, the successful completion of any refit project demands clear communication between all parties involved to ensure everyone is on the same page and understands the individual needs of the boat itself, to reduce the risk of any frustrations arising.
Indeed, many interior crewmembers are quick to express their annoyance at irritating scenarios during refits, such as contractors neglecting to put down dust sheets before beginning their works, causing major damage to painstakingly cleaned and expensive surfaces and creating unwelcome additional work for the crew.
Daniel Küpfer, managing director at Ocean Independence, believes day-to-day problems can be rectified through the thoughtful implementation of a project manager. “No matter whether it is a new-build or refit project, wherever you might be based in the world, you can experience a clash of cultures between the owner and the shipyard’s side, and this can be a source of tension,” says Küpfer. “The solution is to put people there as an interface who understand and can communicate across both cultures to help smooth things over.”
Aldric Bullot, head of customer success at Monaco Marine, agrees. “The shipyard project manager has a vital role to play as the main link between the crew and the yard and contractors,” says Bullot. “They have a huge responsibility for the overall mood of the project. Communication and regular meetings and reporting, as well as being pleasant and respectful of all parties, are key to their role.”
Superyacht crew working out at the Monaco Marine facility. Photo: Guillaume Plisson.
Fantastic facilities
Despite the challenges already outlined, it’s notable that many shipyards have made a significant effort in recent years to ensure crew are supported and are able to rest, recharge and relax during refit periods wherever possible, with their well-being being taken ever more seriously.
Bullot adds, “At our facility, we offer various different places for crew to cook, eat, watch TV and relax, including a crew lounge. We also have a gym area and organise a variety of different activities for them to enjoy during downtime, including yoga classes, bike excursions, paintball, wine tours, beach volleyball and more. We want to make life as easy as possible for crew as we know that the shipyard environment can have a major impact on the well-being of crew.”
Similarly, despite the inevitable change in pace and environment, there is no need for crew to feel isolated from their surroundings during refits. Clelia Frignani, crew services manager at Amico & Co, explains, “The shipyard becomes a new base or berth from which all operations need to be managed. Shipyards need to ensure that as many services as possible are available for crew working on the refit, as well as helping them to ensure their time off when they are here in Genoa, bridging the gap with local knowledge and turning a location into a destination.”
Crew area in La Seyne. Photo: Guillaume Plisson.
As Frignani points out, with the pressure to complete works on schedule constantly ramping up for crew, improving their practical day-to-day experiences during the works is most vital. “On a practical note, the shipyard should provide some separate space for crew use, such as dedicated showers and toilets. At Amico & Co, these are in the marina and can be easily reached with our free shuttle. Spaces are supplemented by the provision of containers that are equipped for support, with temporary galleys and so on.”
From the shipyard’s point of view, there’s also a clear business rationale for boosting crew morale, in terms of reducing employee turnover and keeping a project on track. “Making crew feel welcome here is indeed a large part of our job, so we invest time and energy into getting to know them better,” says Frignani. “This ensures that everyone feels that they are working towards the same goal, getting a great budget and time result for the owner and ensuring that he or she gets to enjoy the yacht as much as possible.”
The knowledge boost
Furthermore, from the perspective of both acquiring knowledge and boosting career progression, getting stuck into a refit project can also have major benefits.
Toby Allies, managing director at Pendennis Shipyard, says, “What is really beneficial for crew involved with refit projects is that rather than just trying to fix something in a very short period of time during an operational period, they actually have the downtime to understand and talk it through with our in-house specialists. This gives them a really positive opportunity to learn the intricacies of the system in detail, and how to maintain it for as long as possible, thus improving their intellectual knowledge of their boat and the systems that keep it going.”
Sean Whitney, captain of 45-metre Dubois ketch Catalina, has worked on both the shipyard and owner’s side in refits, gaining experience at Pendennis on projects including 65-metre sailing yacht Adix and 35-metre Beagle V. This has both enabled his progression up the ranks and is also something he seeks out in his own hiring process for junior crew.
“When doing a refit project, you obviously have to swap your nice shorts, T-shirt and sunglasses for high-vis jackets and steel-capped boots, meaning it is a very different lifestyle, but there is a lot to be gained,” says Whitney. “Personally speaking, I really like refit projects because you learn so much more about your boat and gain hands-on knowledge which you simply would never get otherwise.”
He adds, “If you are looking to become a captain, these projects are excellent for standing out in an interview with an owner. All boats need to be maintained, and you can demonstrate to them that you can handle complex projects and don’t just jump ship at the first sign of difficulty to carry on with the enjoyable sailing part.”
Waterfront Marina in front of Amico & Co’s refit shipyard contains the crew facilities,
including sports pitches and a yoga and pilates studio. Photo: Amico & Co / Carlo Alberto Alessi.
Indeed, it’s worth noting that playing a role in a well-located refit project can also provide a jumping-off point in a crewmember’s future career or aid with the common transition to a shoreside role, thanks to those all-important connections that crew can make, both in the yard and in the local area.
Manuel García, harbour master and production assistant manager at STP Shipyard Palma, says, “Thanks, in part, to our well-connected location in the superyacht hotspot of Palma, working in a shipyard like STP gives crewmembers a very extensive contact book, and they usually change boats after having passed through here. Sometimes they even stop working on board in exchange for a position on land.”
Getting your hands dirty
Bearing in mind all of the above, whether refit is approached with resignation or delight at the end of a busy charter season, there’s a lot to be gained for crew when they are willing to fully immerse themselves in a refit project, accepting the highs and lows along the way.
The final word on the topic can be given to Captain Kelly Gordon. Gordon is at the helm of a 33-metre Pershing which is currently undergoing refit works at Rybovich North in Florida, and she is keen to encourage a hands-on approach from her crew during refits.
“One of my biggest bugbears among my crew is when they say about a task ‘Oh, that’s not my responsibility. I am working in interior, so I can’t help out on deck’. That really grinds my gears,” explains Gordon. “During a refit period, this is the ideal chance to forget what you think your role is, muck in, get your hands dirty and discover new skills which you never knew you had.”
This article first appeared in The Superyacht Refit Report. To gain access to The Superyacht Group’s full suite of content, publications, events and services, click here to join The Superyacht Group Community and become one of our members.
NEW: Sign up for SuperyachtNewsweek!
Get the latest weekly news, in-depth reports, intelligence, and strategic insights, delivered directly from The Superyacht Group's editors and market analysts.
Stay at the forefront of the superyacht industry with SuperyachtNewsweek
Click here to become part of The Superyacht Group community, and join us in our mission to make this industry accessible to all, and prosperous for the long-term. We are offering access to the superyacht industry’s most comprehensive and longstanding archive of business-critical information, as well as a comprehensive, real-time superyacht fleet database, for just £10 per month, because we are One Industry with One Mission. Sign up here.
Related news
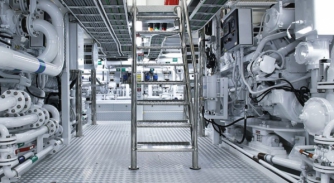
Chief Engineers in sufficient supply
Chief Engineers are enjoying a robust employment market with salaries and rotations moving further in line with expectations
Crew
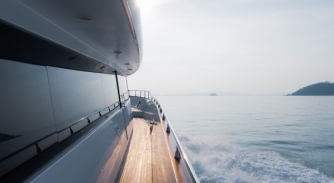
Demand for crew support grows
Calls to ISWAN’s crew helpline have increased with rising trends in reports of poor mental health, unpaid wages and abuse
Crew
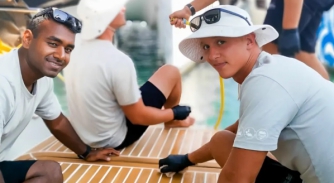
New human rights course for crew
The Progressive Crew Career Programme has launched a new online course to educate crew on their human rights at sea
Crew
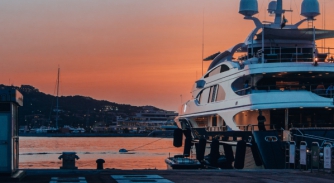
The pregnant flaws
Is it now time to create a culture in which crewmembers feel more secure about their rights regarding pregnancy while working on board?
Crew
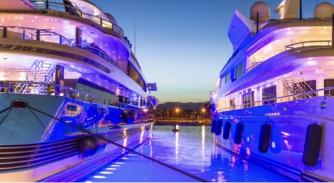
Retention on the rise
Kelsey Purse and Mark Charman of Faststream Recruitment dissect the results of their Superyacht Captain’s Survey
Crew
Related news
Chief Engineers in sufficient supply
1 year ago
Demand for crew support grows
1 year ago
New human rights course for crew
1 year ago
The pregnant flaws
1 year ago
Retention on the rise
2 years ago
NEW: Sign up for
SuperyachtNewsweek!
Get the latest weekly news, in-depth reports, intelligence, and strategic insights, delivered directly from The Superyacht Group's editors and market analysts.
Stay at the forefront of the superyacht industry with SuperyachtNewsweek