Giant leaps
Purposely electing to operate in an environment of extreme pressure is not for the fainthearted, but at Triton Submarines, Craig Barnett finds it offers extraordinary results and rewards…
Pioneering at the forefront of an evolving sector such as human-occupied submersibles requires the capacity to innovate. The challenge for a small- or medium-size business is the efficient conversion of innovative ideas into practical solutions. Creativity is a prerequisite, but there is no substitute for the talent and expertise that are essential to transform revolutionary new ideas into capable and reliable products.
Another essential requirement for innovation is relevant and sometimes proprietary experience, which at Triton Submarines is measured not in years but centuries. Only when a team can repeatedly create and successfully deliver simple, reliable, efficient and safe submersibles is it possible to develop models which challenge conventional thinking but are grounded in practical and common-sense-based solutions.
With the Triton 36000/2 (named Limiting Factor or LF), we set numerous records for exploration in the most remote and least explored area of the ocean – the Hadal Zone, including successfully diving to the deepest point in each of the five oceans during the Five Deeps Expedition. Triton designed, engineered, manufactured and operated the first human-occupied craft in history capable of unrestricted access to the entirety of the world’s oceans. It is not a stretch to compare the ‘repetitive use’ of this remarkable submersible with SpaceX’s development of reusable rockets for space exploration.
Following initial discussion of innovative ideas, Triton follows a path of rigorous design, evaluation and exhaustive testing, with each stage closely monitored by a third-party classification society (DNV GL in the case of the Triton 36000/2). With submersibles being made up of thousands of components this is an arduous process, but with the end product, and its human occupants, operating in the most extreme and hostile environment on Earth, our margin for error is zero.
To illustrate the dedication required to undertake extraordinary innovation, we can use the pressure hull of the Limiting Factor (LF) as an example. This hollow sphere’s task is to accommodate two people, plus all of the non-pressure-tolerant systems and components, on thousands of repeated dives to depths as great as 11,000m. From within the pressure hull, the occupants must be able to see their environment and have full control of all the exterior systems and equipment including propulsion, manipulator arm, navigation, cameras and communications.
Triton’s principal designer, John Ramsay, imagined two Titanium hemispheres, which were clamped and bolted together rather than welded. As counterintuitive as it might have seemed at first, Ramsay’s decision proved both innovative and inspired. When extreme pressure increases risk due to the inherent inconsistency (or discontinuity) of a welded fabrication, a clamped and bolted arrangement between the hemispheres allows for improved tolerances.
In-depth metallurgical analysis proved Grade 5 Titanium to be the best material for the project. Triton and DNV GL sent separate samples of the Titanium to specialist laboratories for metallurgical analysis and the results were compared. Satisfied in the material properties, the hemispheres were forged before precision machining was employed to produce what is essentially a 1,500mm-diameter hollow ball-bearing finished to within 99.93 per cent of perfect sphericity.
Following production was the testing phase, which involved flying the pressure hull to the Krylov State Research Center (KSRC) in St Petersburg, Russia to immerse it in the only test chamber in the world capable of simulating the crushing pressure at ‘full ocean depth’ plus a factor of safety equal to 14,000m or 45,000ft underwater! The 1,740mm inner diameter of the KSRC test chamber had at least partially driven the dimensions of the submersible, so when the sphere was gently lowered into the chamber there were just 30mm to spare on each side of it. Successfully passing these external pressure tests was a milestone moment in the project.
With just one of the components of the Triton 36000/2 ready for assembly, our attention moved to the thousands of other components and systems. Nobody said extraordinary innovation is easy! At Triton we believe the essential key to success in innovation lies in the team employed for the task in hand. It is through curating the most experienced collective of submersible experts on the planet – with almost 500 years’ combined experience in the field - that we have the ability to significantly move the needle in our field.
The Triton 36000/2 project confirmed creativity, experience and intelligence are nothing without determination, dedication and, perhaps most importantly, courage.
We are deeply grateful to our clients who possess a spirit of adventure as well as the courage and passion to explore. It is only through their willingness to fund audacious projects that Triton can create revolutionary submersibles. The intellectual property developed for the LF submersible provided a springboard for many of the new models we have in development now. In order to occupy and maintain a position at the forefront of any sector, a company must be willing to undertake a tireless programme of progression and innovation. Triton is able to deliver submersibles with the reliability, quality and capabilities that we do because we are constantly being challenged by our clients to reach further.
At Triton we carefully consider every move but will always have the confidence in our ability to take giant leaps, which is the nature of innovation. After all, Henry Ford could have just trained faster horses.
NEW: Sign up for SuperyachtNewsweek!
Get the latest weekly news, in-depth reports, intelligence, and strategic insights, delivered directly from The Superyacht Group's editors and market analysts.
Stay at the forefront of the superyacht industry with SuperyachtNewsweek
Click here to become part of The Superyacht Group community, and join us in our mission to make this industry accessible to all, and prosperous for the long-term. We are offering access to the superyacht industry’s most comprehensive and longstanding archive of business-critical information, as well as a comprehensive, real-time superyacht fleet database, for just £10 per month, because we are One Industry with One Mission. Sign up here.
Related news
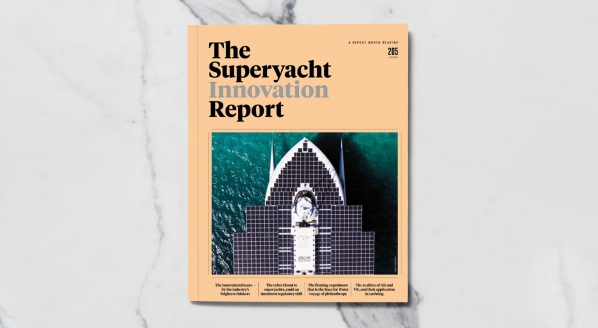
The Superyacht Innovation Report
There has never been a better time, or a greater need, to embrace the future
Technology
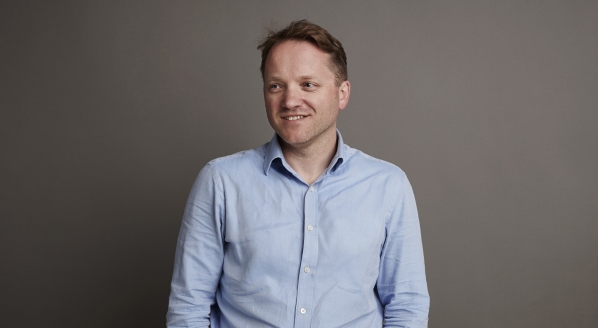
‘Knowledge is the fuel of innovation’
Lateral Naval Architects on its involvement with Oceanco NXT and building the next generation of yachts
Design
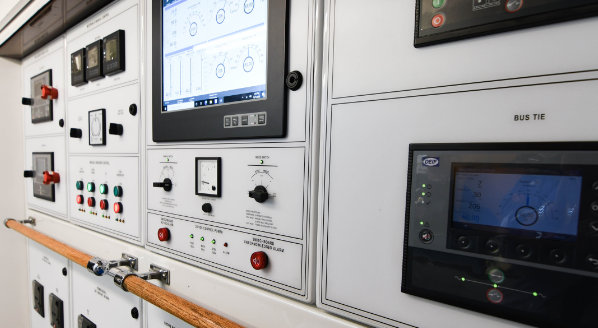
A balance between technology and efficiency
Ward’s Marine Electric’s switchboard automation system updates on-board power management quickly and easily
Technology
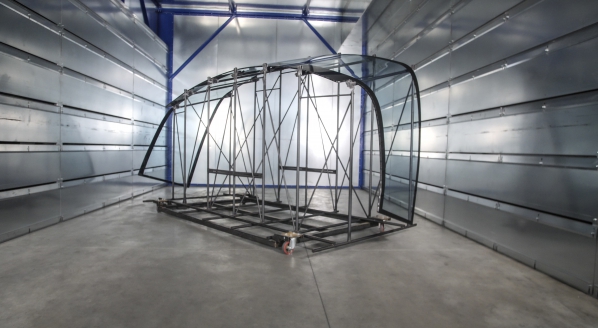
Viraver: modern pioneers in glass
Innovative glass solutions for superyachts that challenge the laws of physics
Technology
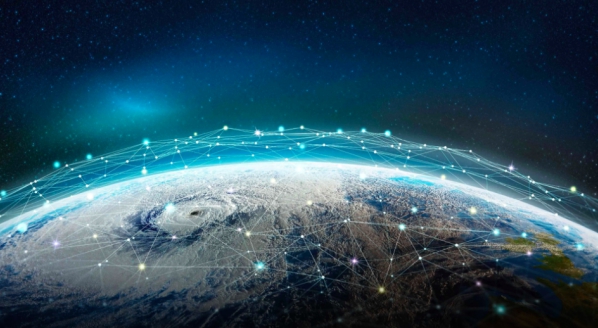
Preparing for the next generation
Plexus Unity answers current challenges in connectivity and prepares for the future
Technology
.jpg)
Introducing Unica
Besenzoni targets the superyacht market with the development of a new brand, Unica
Technology
Related news
The Superyacht Innovation Report
5 years ago
A balance between technology and efficiency
5 years ago
Viraver: modern pioneers in glass
5 years ago
Preparing for the next generation
5 years ago
Introducing Unica
5 years ago
Space-saving and simplicity
5 years ago
Foil-assisted cruising by Baltic Yachts
5 years ago
A homage to the heavy lifters
5 years ago
The importance of innovation
5 years ago
NEW: Sign up for
SuperyachtNewsweek!
Get the latest weekly news, in-depth reports, intelligence, and strategic insights, delivered directly from The Superyacht Group's editors and market analysts.
Stay at the forefront of the superyacht industry with SuperyachtNewsweek