University of Maine 3D prints 8m vessel
The university broke the Guinness world record for the largest printed vessel and the largest 3D-printed solid object…
“Boat building is a long-winded and tedious business, even when what is going down the slipway is a small craft made from modern materials such as fibreglass, rather than something nailed together out of planks of wood. Construct a mould. Build up layers of resin and glass fibre inside that mould. Extract the completed structure and finish it,” explained an article in the Science and technology edition of The Economist. Simplified this description may be, but the journalist has nailed the processes that are so familiar in the construction of superyacht tenders and certain production vessels. However, is a more time and cost-efficient manufacturing process that far away from becoming a reality?
On 10 October 2019, 250 federal and state representatives joined business executives and leaders from University of Maine to witness the UMaine Advanced Structure and Composites Center receive three Guinness World Record for the world’s largest prototype polymer 3D printer, the largest solid 3D-printed object and the largest 3D-printed boat.
The 3Dirigio, as the vessel is known, is eight metres long, 2.2 tons and took 72 hours to make, thanks to the use of an enormous 3D printer. Indeed, according to the University of Maine, the new 3D printer is designed to print objects as large as 30m long, 6.7m wide and three metres high, which, if you ignore the height restrictions, is near enough the minimum requirements for a vessel to be described as a superyacht.
While height is a clear issue, it is not unfathomable that modular sections up to three metres high could be printed, nor indeed that the printers of the future will not be bound by such restrictions. While 72 hours represents a dramatic reduction in build time, researchers also believe that the use of such technology, once it becomes more widely available, will also dramatically reduce build costs.
If the idea of printing superyacht tenders, or indeed superyachts, doesn’t sound as farfetched as it did a few years ago, the UMaine Advanced Structure and Composites Center has another trick up its sleeve.
The ‘ink’ used for the printing process is in fact a molten thermoplastic resin that contains carbon fibres. Neither plastic nor carbon are desirable building materials when one considers the environmental foot print of a product. The university, therefore, intends to use natural local resources to replace the carbon fibres with cellulose fibres sourced from New England’s vast sustainable forestry industry. The aim, according to a spokesperson from the Composites Center, is to 3D print with a material that contains 50 per cent wood matter and that would be of equivalent strength and weight to aluminium. The hulls created by such a material could also be recycled and used again for future projects.
It may yet be some time until the industrial use of large 3D printers becomes common place. Indeed, it will still be a number of years before such technology is taken on by early adopters. However, the benefits of such technology are clear to see.
NEW: Sign up for SuperyachtNewsweek!
Get the latest weekly news, in-depth reports, intelligence, and strategic insights, delivered directly from The Superyacht Group's editors and market analysts.
Stay at the forefront of the superyacht industry with SuperyachtNewsweek
Click here to become part of The Superyacht Group community, and join us in our mission to make this industry accessible to all, and prosperous for the long-term. We are offering access to the superyacht industry’s most comprehensive and longstanding archive of business-critical information, as well as a comprehensive, real-time superyacht fleet database, for just £10 per month, because we are One Industry with One Mission. Sign up here.
Related news
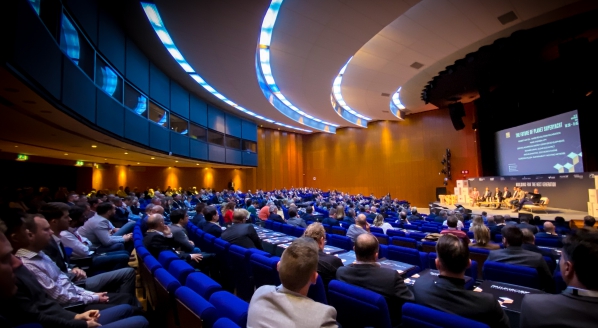
Nobility of purpose
The drive to counteract the nefarious perception of the superyacht industry is a unanimous goal
Business
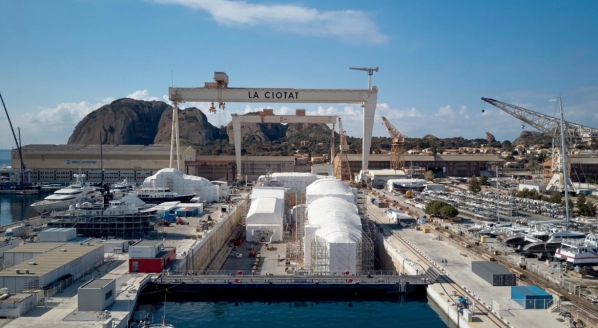
Refitting the next generation
An interactive discussion on how requirements for refit infrastructure are changing will take place at TSF
Business
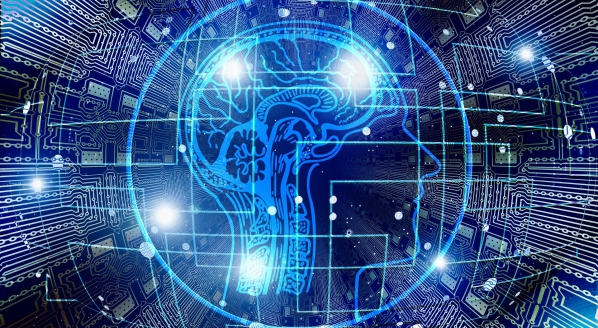
How can artificial intelligence improve the superyacht industry?
A discussion on how the technology fits into superyacht design, building and operations will take place at TSF 2019
Technology
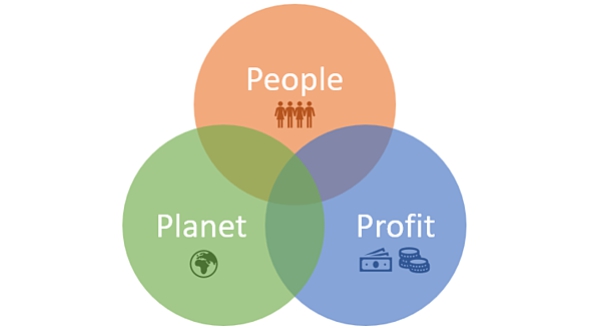
Time to re-evaluate your bottom line?
The concept of triple bottom line and what the superyacht industry could learn from it
Business
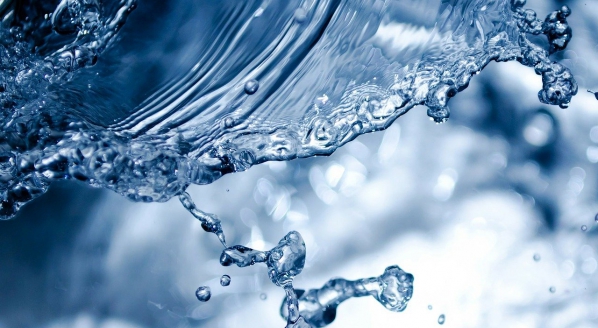
FMD launches new wastewater treatment solution
The Sequencing Batch Reactor is an environmentally-responsible solution for wastewater treatment at sea
Technology
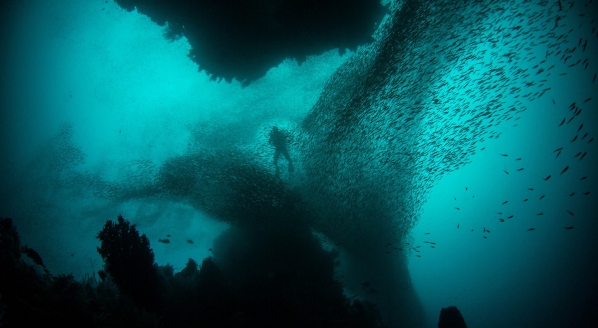
The Art of Business
Technology entrepreneur Jasper Smith will open The Superyacht Forum 2019
Business
Related news
Nobility of purpose
5 years ago
Refitting the next generation
5 years ago
Time to re-evaluate your bottom line?
5 years ago
FMD launches new wastewater treatment solution
5 years ago
The Art of Business
5 years ago
Choosing eco-friendly cleaning products
5 years ago
NEW: Sign up for
SuperyachtNewsweek!
Get the latest weekly news, in-depth reports, intelligence, and strategic insights, delivered directly from The Superyacht Group's editors and market analysts.
Stay at the forefront of the superyacht industry with SuperyachtNewsweek